Manufacture of industrial electronics
We develop and manufacture products for demanding industries in the range from individual electronic boards through assemblies to the production of functional units. We manufacture electronic assemblies according to production documentation and specific designs and requirements of our customers. We also develop our own SandRA control systems, which ZAT applies to projects in a number of fields.
Our products are used in Turkey, South Korea, China and Europe. Their quality, reliability and longevity are ensured by top equipment and precisely set technological processes.
SMT mounting
The state-of-the-art automatic production lines we use ensure the smooth running of all the steps needed to create a flawless product. These lines can fit all currently known component housings and are also ready for future developments in the field of electronic boards.
3 automatic lines for flexible operation
Thanks to the optimal number of automatic lines, we are able to constantly meet the requirements of our customers. At the same time, we are able to produce medium series production, piece production and prototypes at the same time.
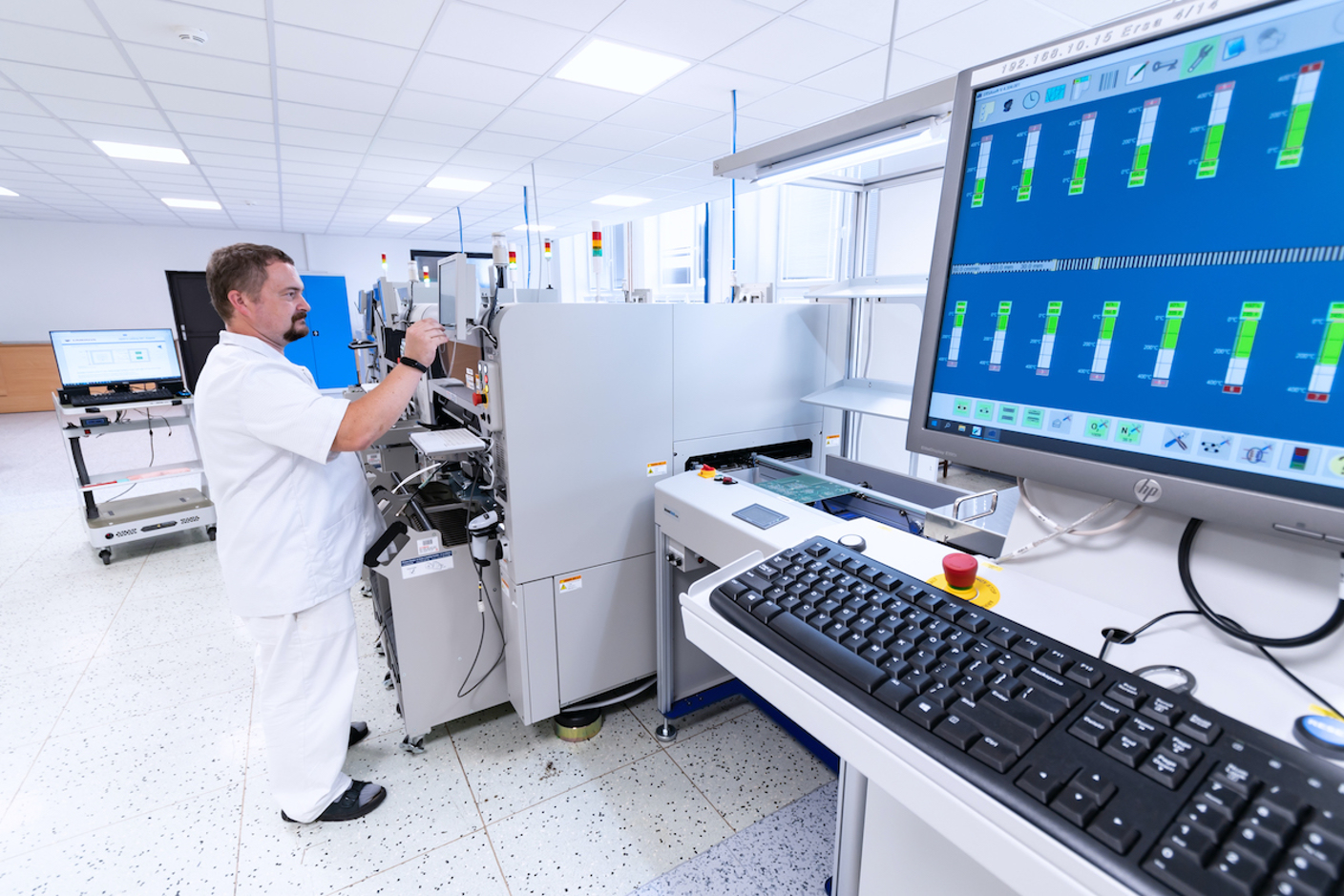
Automatic optical inspection
Checking the solder paste printing
Before mounting the board and soldering, it is essential to check the application of the solder paste. At this crucial moment, the automatic optical inspection evaluates the amount of paste used in the 3D dimension and eliminates the possibility of errors caused by the human factor.
Checking the mounting and soldering of components
To ensure the maximum quality of the product, the device automatically checks the mounting correctness of the component - its type, polarity, coplanarity and soldering.
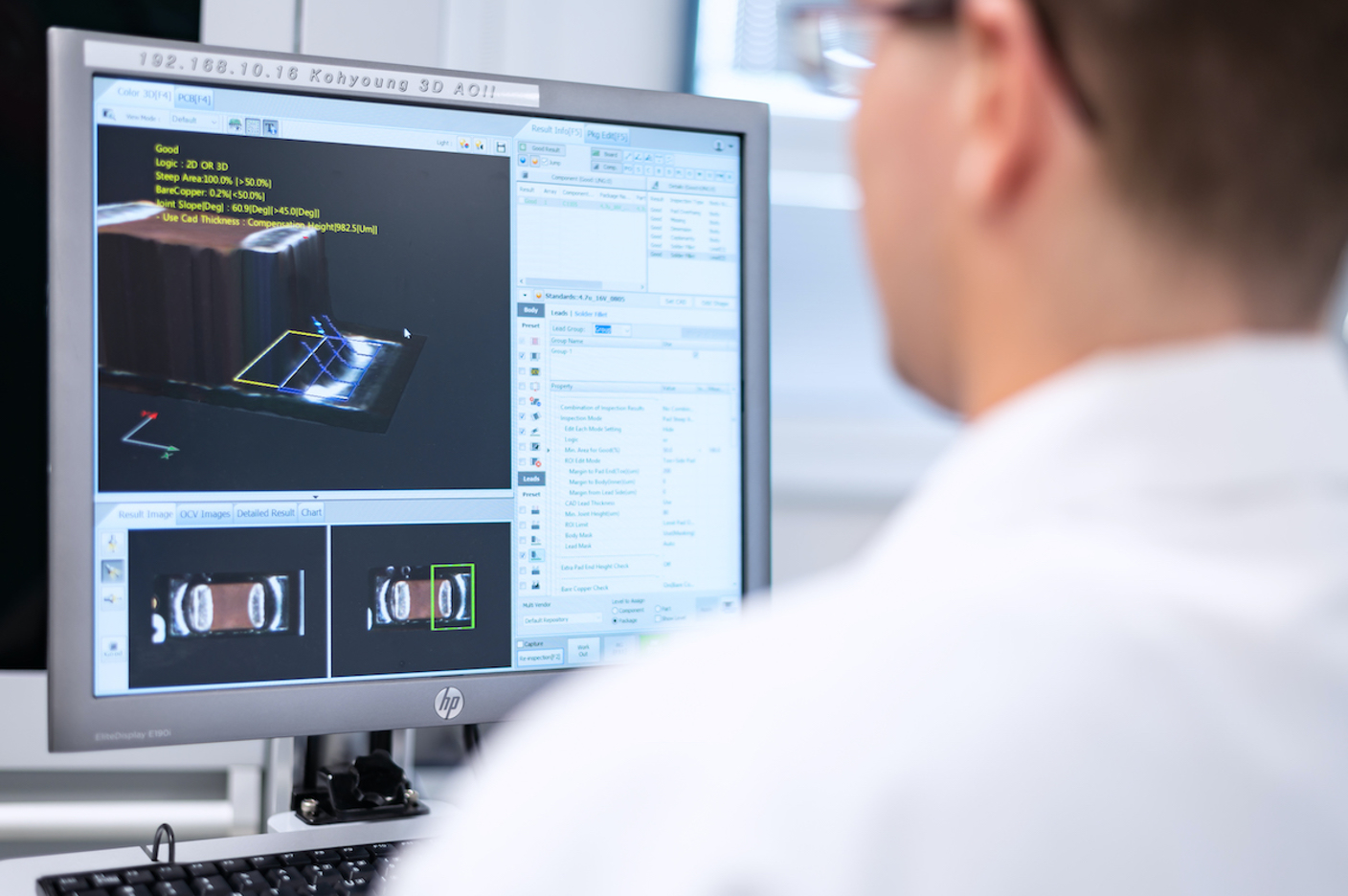
Two types of soldering
We produce electronic boards with high integration and all soldering processes are controlled. We use a standard soldering wave with a dynamic soldering nozzle for mass soldering. In the case of a large assortment of soldered components within one product, we use the possibility of selective soldering. Both types of soldering processes are covered with an inert atmosphere, which increases the durability of the soldered joint and ensures a longer product life.
X-ray control
We are equipped with non-destructive X-ray diagnostics for the installation and soldering of BGA packages. The control of products and production operations obey the standard IPC-A-610E class 3.
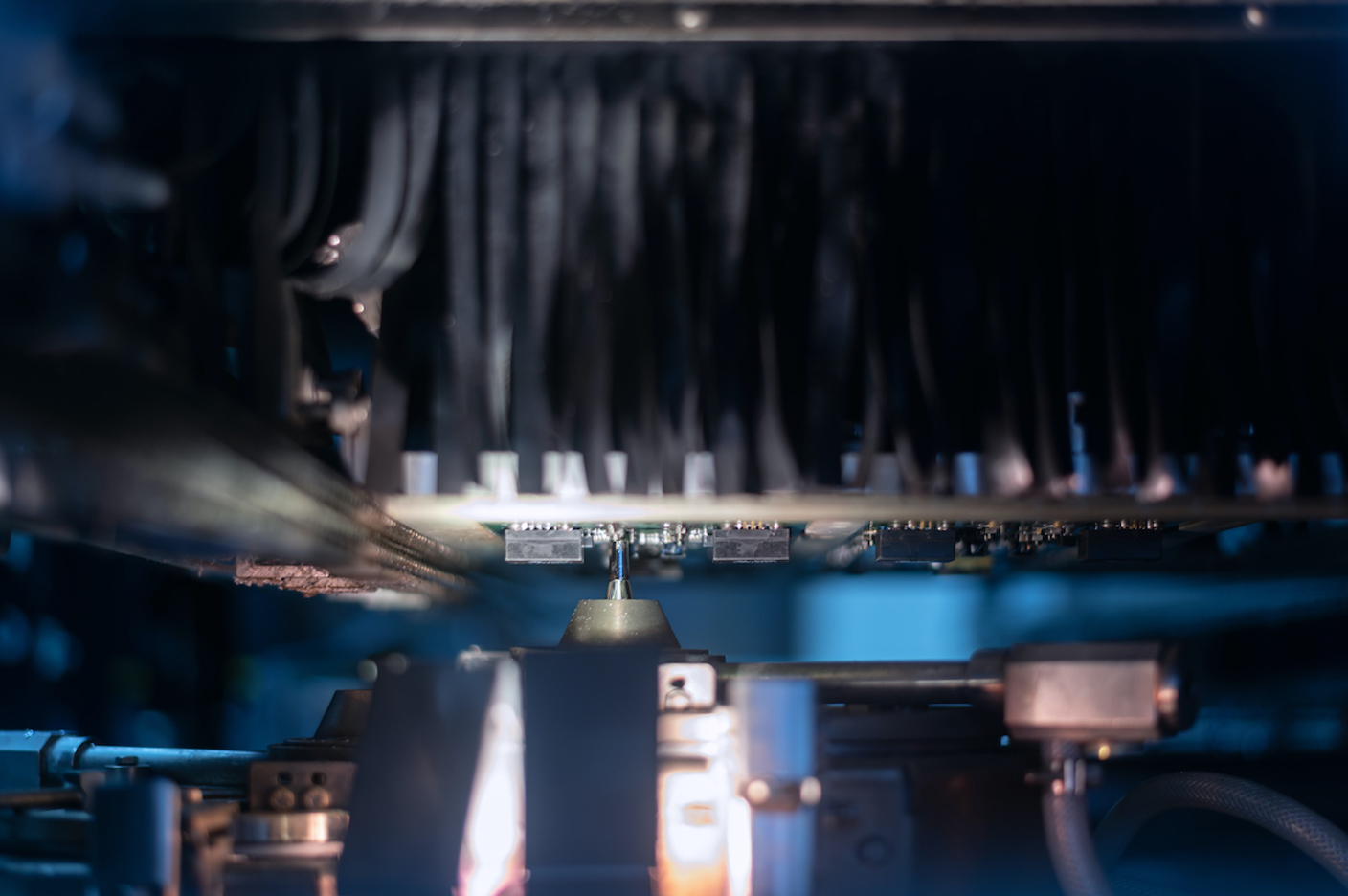
Cleanliness and varnishing
Washing, rinsing and drying
The aim of the process is to remove all technological impurities from the boards and to wash out gaps up to 10 μm.
Varnishing with selective coating technology
We use selective varnishing technology for the application of protective varnishes, thanks to which only those surfaces and components required by the customer can be varnished.
In accordance with the requirements of ČSN EN 50155 standards, we provide requirements for the climatic resistance of manufactured components.
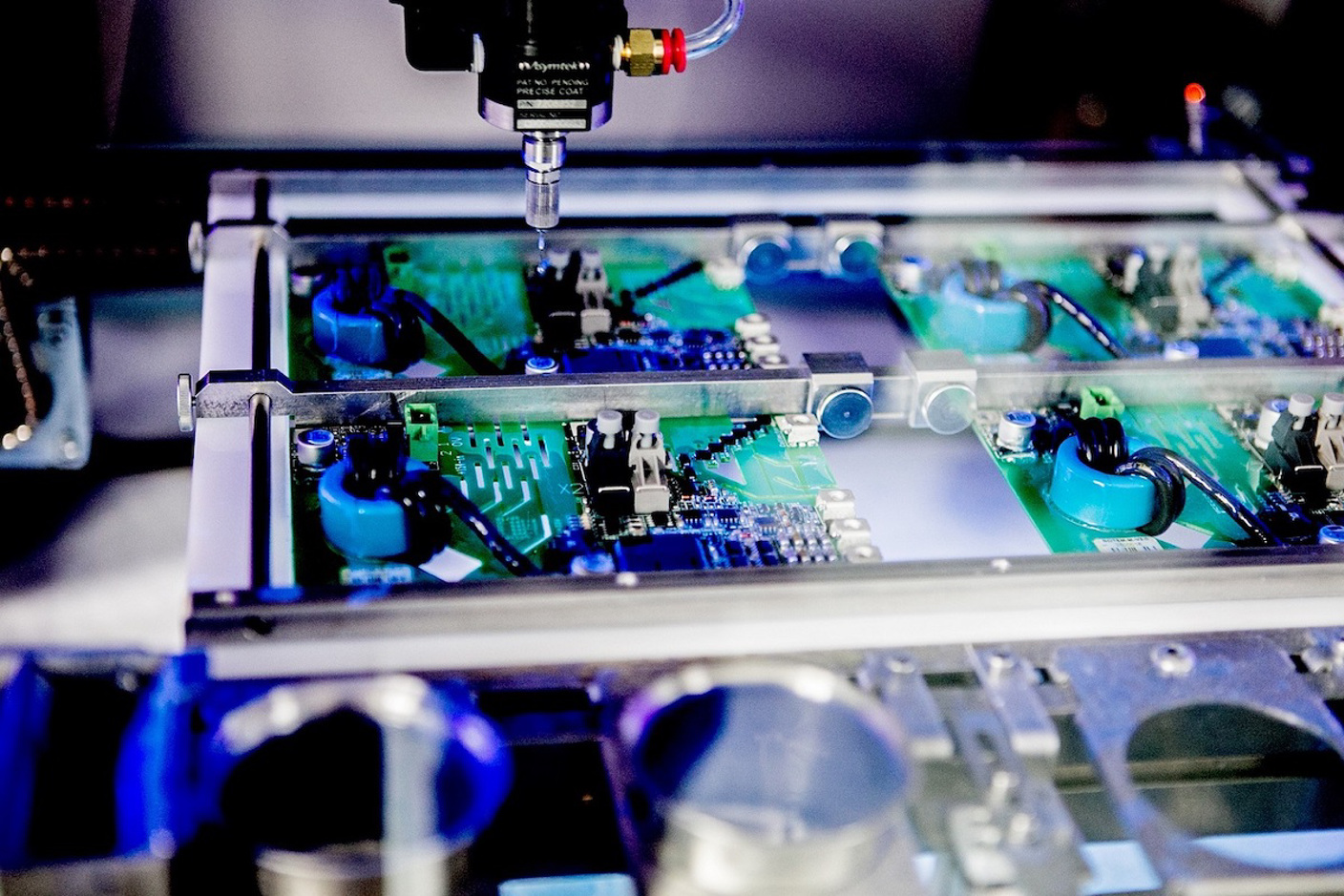
Control systems and cabinets
We assemble higher units of control systems, such as processor stations, controllers or inverters into switch cabinets. We use a series of cabinets from the selected supplier KORAMEX or from renowned manufacturers, such as Rittal,, OEZ, Schrack TVD, for the assembly of cabinets.
Production of cabinets
Control system cabinets
We manufacture and assemble cabinets according to the customer's tender documentation with our own control system (SandRA) or with the control system of other renowned manufacturers (SIEMENS, B @ R, SAIA, AllenBradley, etc.)
LV cabinets up to 1KV
As a standard, we implement cabinets for the control of technological processes, as well as distribution cabinets and special cabinets, eg for generator or telemetry station excitation.
Functional tests
Testing of electronic assemblies
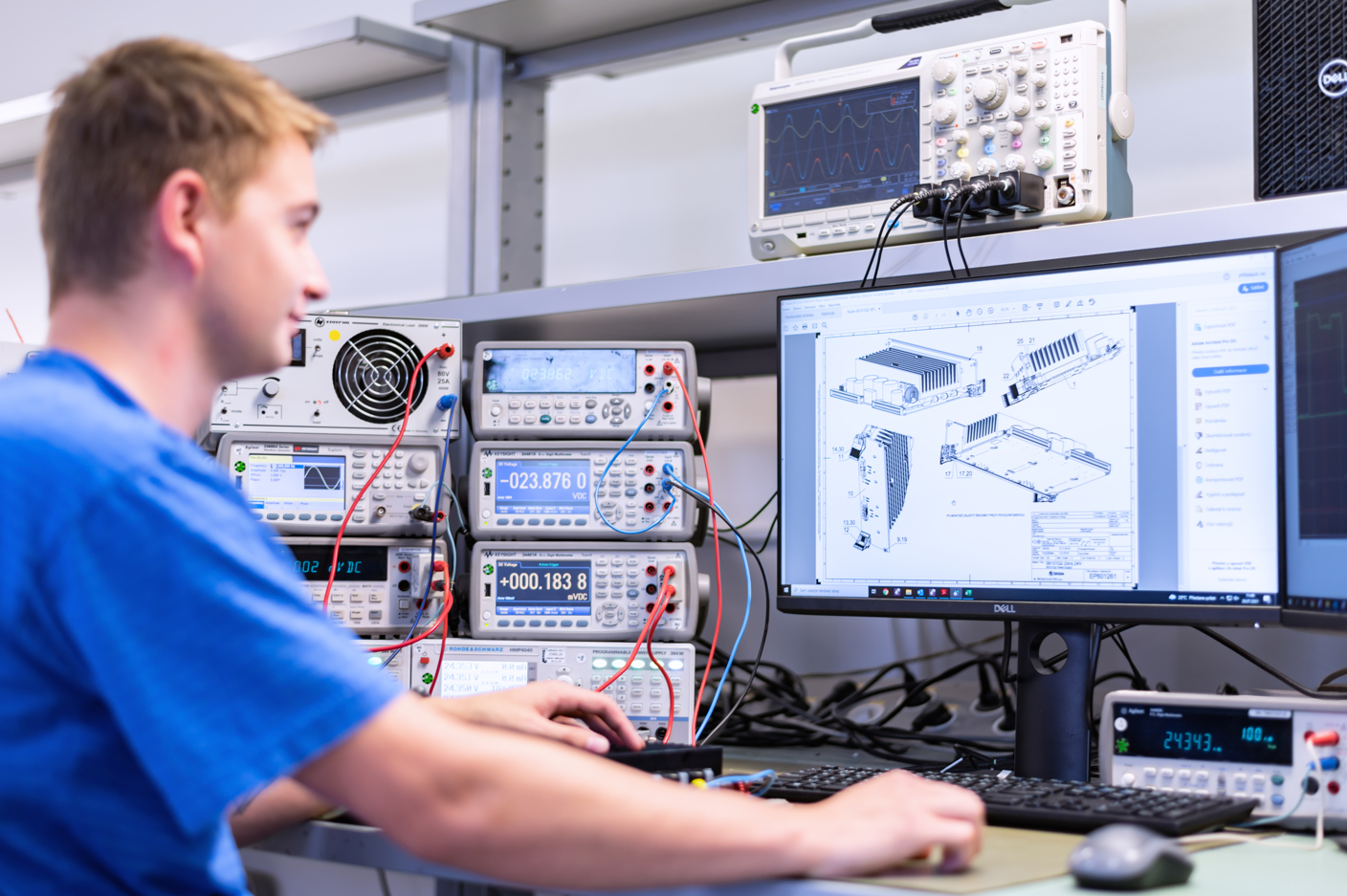
We subject the manufactured assemblies to functional tests to the required extent. When testing units, automatic testing workstations are usually used, which eliminate the human factor and guarantee accurate measurements with records. Automatic testing also brings increased efficiency of tested products and time savings.
After the tests, a test report is automatically created, including authorization, which we provide to the customer.
Testing of higher units
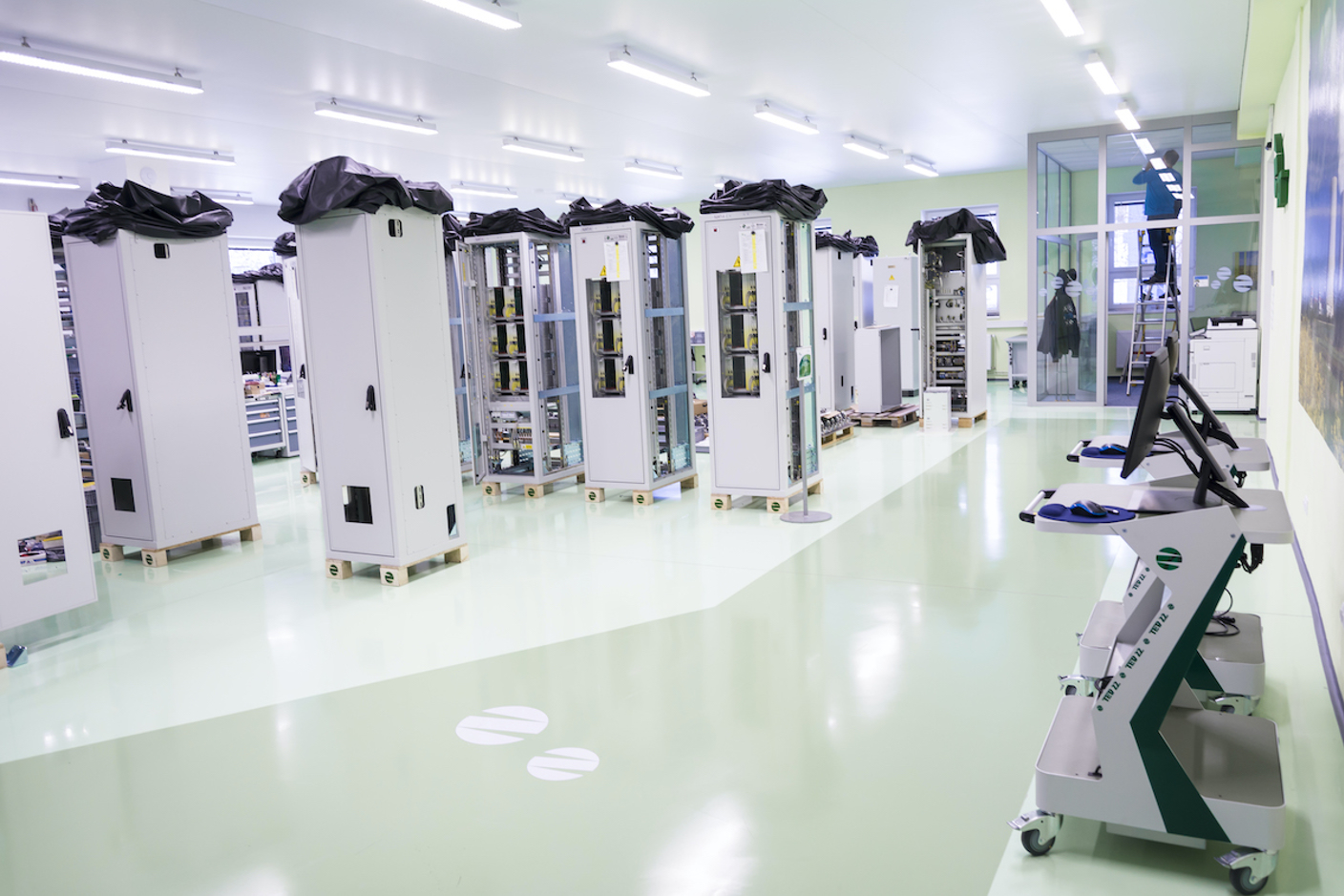
The electronic assemblies are installed into cabinets, which are followed by Factory acceptance tests (FAT), the aim of which is to verify the correctness of the execution at the place of production on the basis of design and compliance with the project documentation. In this validation phase, we perform series of tests (functionality of control system inputs and outputs, functionality of selected algorithms, functionality of communications) within the delivered project.
Subsequently, a Site acceptance test (SAT) is performed to verify compliance with the required parameters at the installation site together with the end customer.
Want to know more? Contact us!
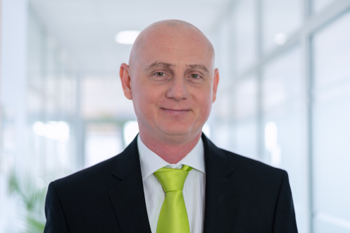